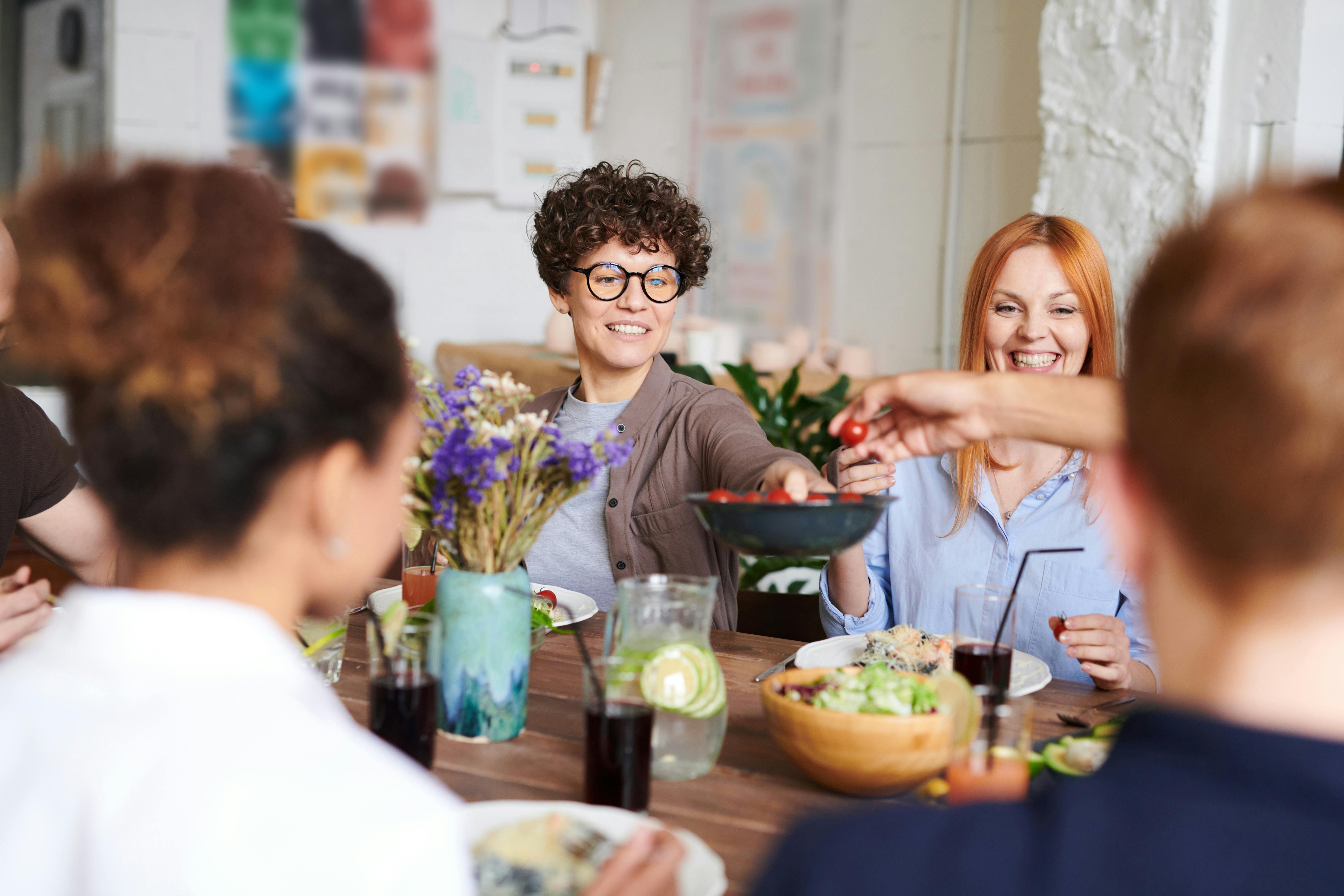
How Long Does Cement Take to Dry?
The Cement Drying Process
Understanding **how long does cement take to dry** is crucial for any construction project. The **cement drying process** involves several stages, including setting, hardening, and ultimately achieving full cure. **Curing time for cement** can vary significantly depending on the conditions under which it is placed. When poured, fresh concrete goes through different phases - first the setting time, where it becomes firm enough to bear weight, and eventually the hardening phase, culminating in the **full cure time for cement**. In ideal conditions, this entire process can take from a few days to several weeks.
Time for Cement to Set
The **time for cement to set** typically refers to how long it takes for the mixture to firm up. Generally, initial set times can range from 30 minutes to a few hours depending on factors like the type of cement used and the environmental conditions. Once set, the subsequent **drying time of cement** ensures that the mix reaches its desired strength, which usually takes about 28 days for standard Portland cement. Various elements, such as humidity and temperature, significantly influence both the setting and drying times.
Best Practices for Cement Curing
To achieve optimal results, implementing **best practices for cement curing** is vital. Proper curing helps maintain moisture in the cement mix, thus promoting hydration and strength development. This can include covering the cement with wet burlap or using curing compounds to keep the surface moist. It's important to avoid allowing the surface to dry out prematurely to minimize cracking and ensure adequate **cement hardening duration**.
Factors Affecting Cement Drying
Various **factors affecting cement drying** include temperature and humidity. For instance, hot weather can expedite the evaporation process, leading to **issues in drying concrete** if not controlled properly. By maintaining the right environmental conditions and knowing **the impact of temperature on cement**, contractors can modify their strategies to ensure efficient drying rates and optimal strength development.
Drying Conditions for Concrete
The **drying time for concrete** greatly depends on the surrounding climatic conditions. Understanding these **drying conditions for concrete** can help predict the time needed for the cement to properly dry and cure. Consistently measuring and controlling temperature and humidity around the fresh concrete can boost overall results. For instance, **cement drying indoors** may happen quicker due to controlled environments, while **outdoor cement drying time** can vary widely based on weather changes.
Cement Drying Temperature
The **cement drying temperature** plays a critical role in hydration. Ideal temperatures range between 50°F to 85°F (10°C to 29°C). On the other hand, if it’s too cold, such as during **cement drying in winter**, the hydration process slows down, which can also lead to strength deficiencies. Utilizing heating blankets or insulated curing methods can help mitigate the effects of colder environments and accelerate drying times.
Moisture Effects on Cement Drying
Understanding how moisture levels can impact the drying process is crucial. High humidity can hinder the effective drying of concrete, leading to **cement drying issues** like efflorescence, where salts form on the surface. Conversely, very low humidity can enhance drying rates unexpectedly, stressing the importance of adjusting to environmental factors. Monitoring these conditions helps in maintaining an effective **drying concrete** environment.
Rapid and Slow Curing Cement
Different types of cement have varying **drying times**. For instance, **rapid drying cement** is formulated to set quickly, which is advantageous for projects that are time-sensitive. Conversely, **slow curing cement** might be preferred in scenarios where gradual strength development is necessary, allowing for better management of heat and hydration, especially in expansive climates. Knowing which to use can significantly impact project timelines and structural integrity.
Common Mistakes in Cement Curing
<pIt's easy to make errors during the cement drying and curing process, particularly in haste. Some **common mistakes in cement curing** can lead to poor outcomes, such as cracking or insufficient strength development. Educating oneself on these pitfalls can mitigate risks and enhance overall project success. Understanding the stages of hydration and maintaining moisture levels are essential components of proper curing practices.Concrete Moisture Control
Concrete moisture control is vital for preventing defects and ensuring that the final product meets strength standards. Mismanaging moisture can lead to rapid drying and the formation of cracks. One practical approach is to install moisture meters or sensors to continuously monitor the conditions surrounding the newly poured concrete, enabling timely adjustments to the curing techniques being implemented.
Troubleshooting Cement Drying Issues
Troubleshooting **cement drying issues** can often save both time and resources. If static or slow drying is detected, consider evaluating the environmental factors, initial mix ratios, or compounding during the mix. Identifying potential flaws early can help adjust the **curing methods for cement** to boost process efficiency and ultimately enhance structural strength.
Innovative Curing Techniques
Advancements in **innovative cement applications** can also contribute to the drying process. Utilizing additives that control drying times and modern curing compounds can make curing more effective. One such technology includes **hydrophilic admixtures**, which not only attract moisture but also increase the effective curing time, helping in the **hydration of cement** and safeguarding against premature drying.
Key Takeaways
- The ability to accurately predict **how long does cement take to dry** is vital for construction scheduling.
- **Factors affecting cement drying** include temperature, humidity, and moisture levels.
- Proper curing practices and techniques can significantly enhance cement strength and durability.
- Awareness of **common mistakes in cement curing** can prevent costly errors on site.
- Utilizing innovative curing techniques can optimize the **cement drying process**.
FAQ
1. What are the ideal humidity conditions for cement drying?
The ideal humidity for cement drying is generally around 50-70%. Too much moisture can prolong the drying time, while too little can cause cracks. Maintaining a balanced humidity level is essential for effective curing.
2. How can I speed up the cement drying process?
To speed up the drying process, you can use **rapid drying cement**, control environmental temperature, and use heaters or fans to circulate air around the cement. Also, avoiding large masses of concrete can help reduce overall moisture retention.
3. What are the effects of temperature on cement curing?
Temperatures above 85°F can accelerate drying, which may lead to issues like cracking. Conversely, temperatures below 50°F can slow hydration, prolonging **curing time for cement**. Thus, controlling temperature is critical for successful curing.
4. How does moisture affect cement's strength development?
Moisture is essential for the hydration reaction in cement, which contributes to **cement strength development**. Insufficient moisture can lead to lower strength outcomes, making proper moisture control key in the curing process.
5. Can I pour concrete during winter?
Yes, but extra precautions are necessary during winter. Use insulated coverings or heating blankets to maintain optimal temperatures and prevent the water in the mix from freezing, ensuring proper hydration and curing.
6. What monitoring techniques can help avoid curing errors?
Utilizing moisture meters, thermometers, and even laser-scanning technology can help monitor the concrete’s drying environment. Regular assessments allow for timely adjustments in **curing methods for cement** and help to ensure the desired outcomes.
7. Can I use additives to control cement drying times?
Yes, additives such as retarders and accelerators can modify drying rates. Retarders slow the **setting time of cement**, while accelerators do the opposite, allowing for customized control depending on project requirements and environmental factors.
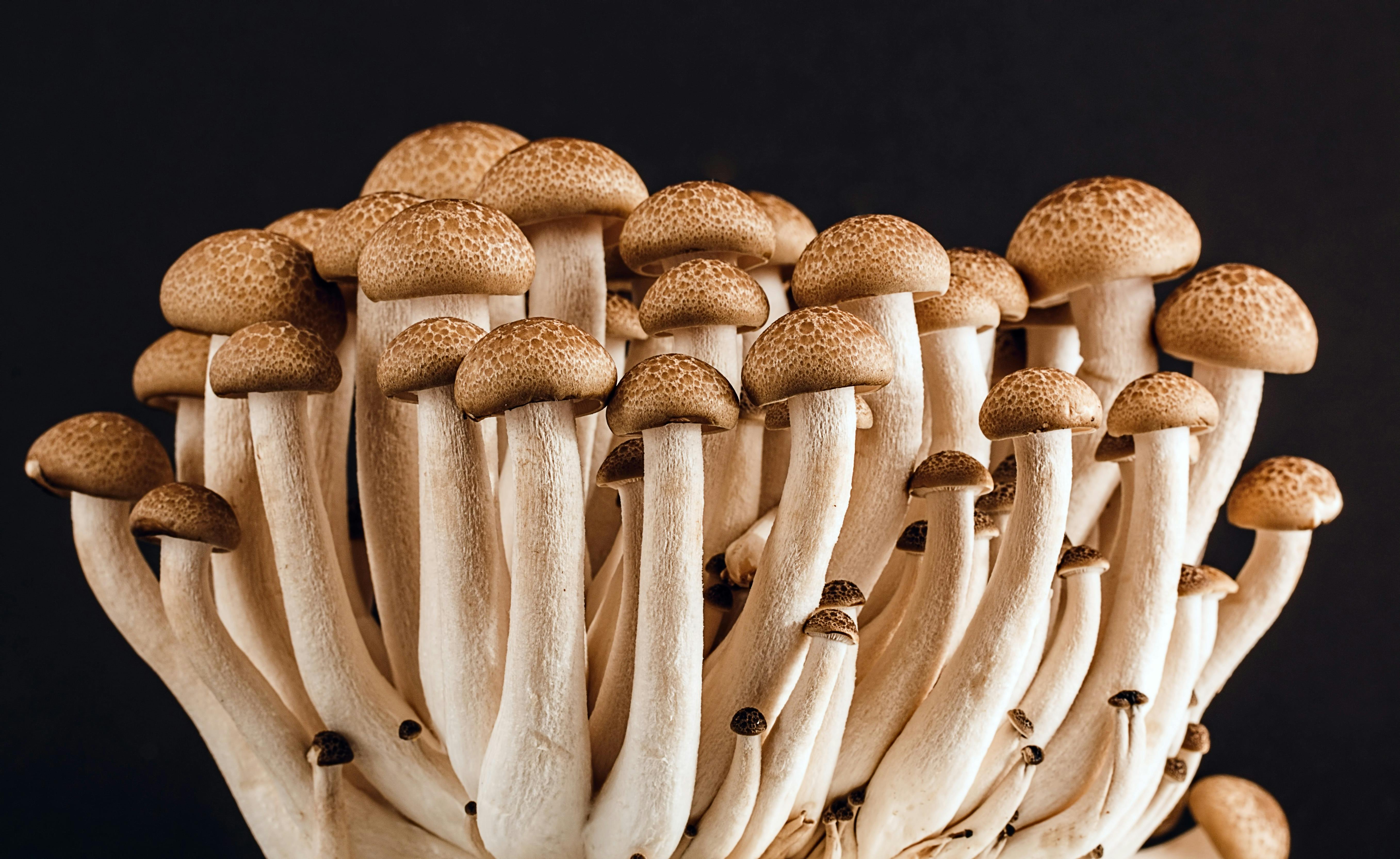
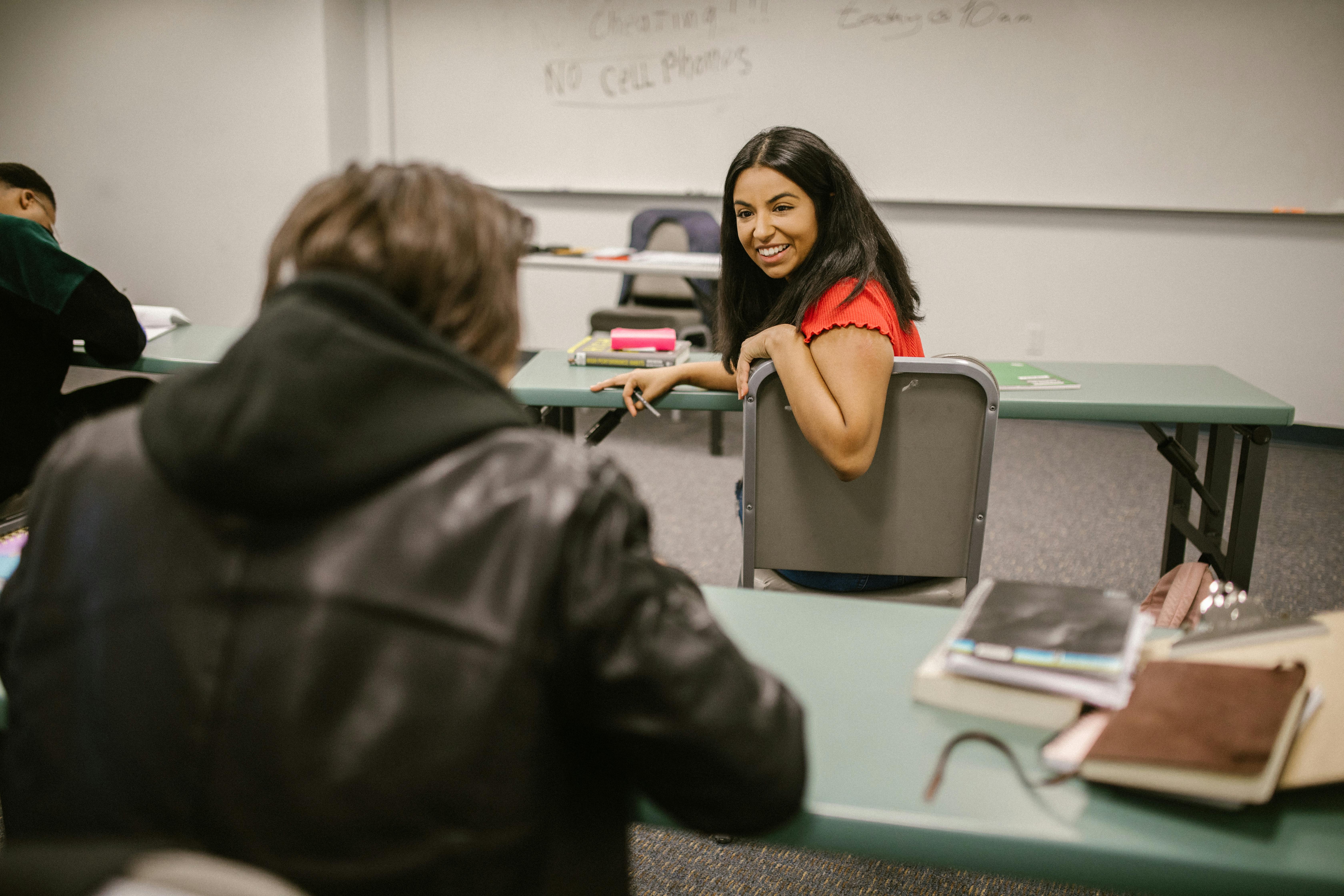